US shipbuilding challenges a matter of national defense
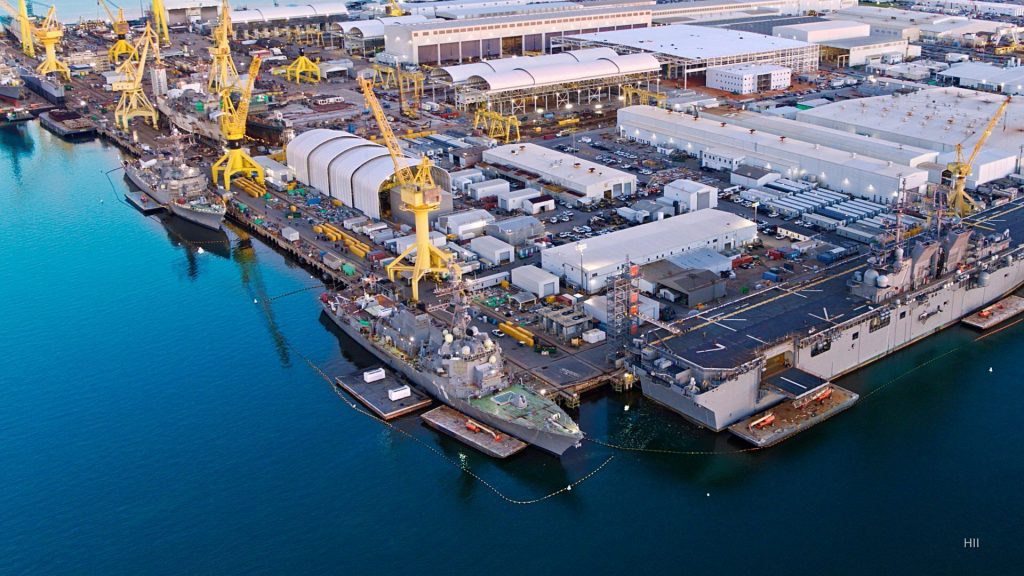
During World War II, more than 1 million people worked in American shipyards. Now, fewer than 200,000 of these jobs remain nationwide.
“We’ve been mired in bureaucratic inertia, budgetary gridlock in Congress and chronic shortfalls in shipbuilding investment,” Secretary of the Navy John Phelan said in a speech at the April 2025 Sea Air Space Breakfast. “…Our adversaries have been building and getting better.”
Renewed focus across government and industry
It’s a problem not just for the U.S. economy, but for its national defense as well. Right now, the U.S. Navy has fewer than 300 warships in its fleet. The service is trying to expand the fleet to 381 over the next 30 years.
“China constructed more ships last year alone than we have since World War II,” Phelan said. “China is not interested in being number two. They are attempting to dominate the seas and beyond that, the global order. Our competitors are not waiting for us to get our act together. They see weakness, and they will try to exploit it.”
It’s not just Phelan who highlighted the importance of keeping pace with China at sea. It’s been a theme in Navy circles for a while.
“The conversation is louder than it’s been, and it’s happening in Congress and in the White House and in the industry,” Admiral James Kilby, acting chief of naval operations, said on April 9. “So this awareness seems to be higher, at least by my recollection, than I recall in the past, but it’s going to take a national effort to get after it.”
Phelan’s focus on shipbuilding is welcome news for Navy leadership, who have often been at odds with Congress about the best way to meet the demands put on the maritime forces.
Modernizing the fleet: New builds and repairs
Hitting the Navy’s goal of 381 warships in the next three decades will require not just new construction, but additional work to keep the ships currently sailing operational for as long as possible.
“I’m a cruiser sailor. I love cruisers. We’ve had them for a long time. My ability to keep them at sea, to do that mission is challenging, increasingly challenged, because of HME hull cracking and tank cracking,” Kilby said. “So to me, if I can’t keep that ship at sea, it’s of no use to the command, commander or the president or the secretary of defense.”
The increased attention on shipbuilding isn’t happening in a vacuum. Many of the players in the industry saw this coming and were proactive in trying to meet the need. Included in that supply chain are companies like Fairbanks Morse Defense.
The Wisconsin-based manufacturer makes all sorts of parts and fittings that go on U.S. warships. Some upkeep can keep a ship out of service for months.
“You open things up, you do an inspection, you write a report. That report then has to go up and through several people and get approved, and then it comes back down and they say, ‘Go,'” Keith Haasl, president of service and technology at Fairbanks Morse Defense, said. “And then you might need parts. You might need machine capability, you might need additional resources that you don’t have set up.”
As the process goes on, there’s “lots of delay opportunities and lots of opportunities for long-term problems like parts availability,” Haasl added.
So, the company created its Pit Stop strategy, where repair crews bring pretty much the whole shop to the ship.
“We bring all the mandatory replacement parts that we have for the activities we plan,” Haasl said. “We’re also bringing contingency parts along for the things that you know might bite you when you get into the process. And how we do that then is, instead of sending a report up and waiting for a response every day, we meet with the right folks and we talk about those and we can approve it that fast, and we can move that fast so everything’s adjudicated in real time, and it allows us to keep moving.”
Programs like Pit Stop aren’t possible without deep pools of talent and resources. That’s why Fairbanks Morse Defense’s CEO George Whittier said the Navy should look to companies like his more often.
“I have about 1,500 employees, we are not labor-constrained,” Whittier said. “And there is a tremendous opportunity to take work out of the shipyards and bring that into the Midwest, and start to get more work done…. I don’t think we’re utilizing the Mississippi River at all, and so we could look at: how do we make equipment? How do we make modules? How do we do things, put it on barges, send it down to the Gulf, send it wherever it needs to go so that the shipyards themselves can become more of an assembly plant, rather than a fabrication plant?”
Digital transformation in shipyards
Turning shipyards into fabrication plants isn’t impossible, but it would first require bringing those shipyards fully into the digital age.
At Huntington Ingalls Industries’ Newport News Shipbuilding division, that job falls to Colleen Graham, the chief of AI and digital innovation.
“AI, digital data management, all of these modern technical capabilities are the 21st-century equivalent of Henry Ford’s factory lines and whatnot of the 1930s,” Graham said.
As the largest manufacturer of U.S. warships, Graham said it’s absolutely critical Huntington Ingalls Industries adapts to the latest technology, otherwise it risks insolvency.
More than half of the companies counted on the Fortune 500 list in 2003 don’t exist anymore — and a lot of that is because of the digital disruption.
To succeed, Graham said, businesses can’t chase “shiny objects.” They have to solve real-world problems, like making sure all of the equipment in the manufacturing process gets a digital upgrade so the work can be monitored.
“The tech-geek term for that is Industrial Internet of Things,” Graham said. “Very little IIoT capability in the shipyard… I’m a data scientist, all the data scientists for NNS work for me, and they want to do data science, but you’re not going to be doing any machine learning or any AI when you don’t have the data. So it was very critical to actually launch a program, which we called Digital Plant, to start to connect equipment up so that we could get the data flowing.”
Graham said through a Digital Plant pilot program at HII, her team originally expected to see a 30% increase in output, but saw a 50% increase instead, which sets the project up as sort of “lighthouse” that the industry can use to chart new paths of innovation.
Still, even with all the innovations AI might bring to shipyards, and even if the U.S. shipbuilding industrial base diversifies enough to include more suppliers from around the country, it might not be enough to hit 381 naval warships in the next 30 years.
This is why foreign companies like HD Hyundai Heavy Industries could be called on to play a role in building America’s future fleet. The South Korean shipbuilder is already the world’s largest. It built Aegis-enabled warships for South Korea that are very similar to U.S. guided missile destroyers.
Hyundai Heavy Industries said it can build up to five of the vessels every year for the United States Navy.
While the U.S. doesn’t typically like to have its warships built by other nations, it’s not necessarily opposed to the idea either.
Hanwha, another South Korean shipbuilder, just performed maintenance on a United States naval support vessel.
Pulling from his business background, Phelan said at this point in the planning process, there are no bad ideas when it comes to revitalizing U.S. shipbuilding.
“This is a big, big priority for the president, and he is extremely focused on it, and I certainly don’t want to disappoint him,” Phelan said. “If I do, you’ll probably have another (secretary of the Navy) here in a year or two.”